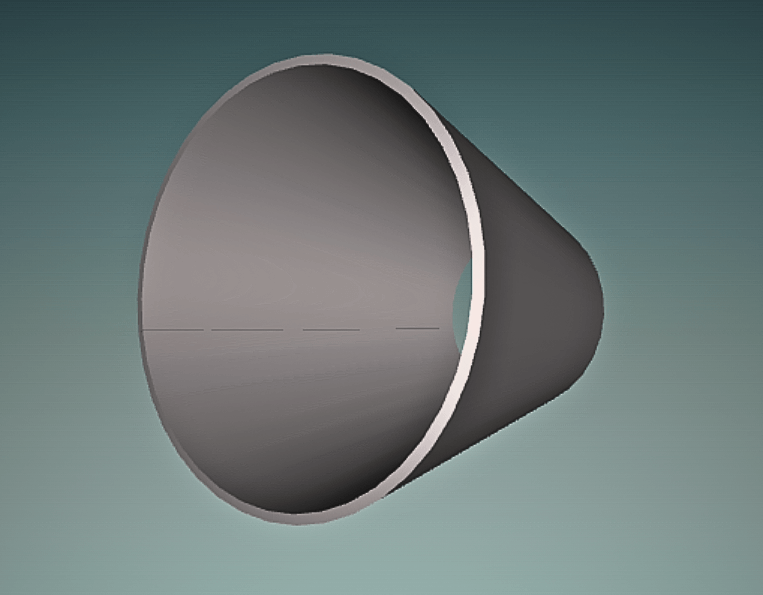
In the realm of industrial fabrication, the creation of cones and reducers stands as a testament to precision engineering and meticulous craftsmanship. These components, essential in various applications ranging from piping systems to pressure vessels, demand specialized techniques for their formation. In this blog post, we delve into the intricate processes of fabricating cones and reducers, highlighting the nuances between bending and pressing methodologies.
Bending: Crafting Large Diameter Cones/Reducers
Bending represents a fundamental method employed in the fabrication of cones and reducers, particularly for components with comparatively large diameters. This process allows for the creation of cones and reducers in either single-piece or two-piece configurations, catering to diverse structural requirements and design specifications. By leveraging bending techniques, manufacturers can achieve seamless curvature and dimensional accuracy, ensuring optimal performance in industrial settings.
Pressing: Precision for Smaller Diameter and Higher Thickness Components
In contrast, pressing emerges as a preferred technique for manufacturing cones and reducers characterized by smaller diameters and higher thicknesses. This method employs male and female dies to shape the material, offering enhanced control over geometrical intricacies and wall thickness variations. With pressing, manufacturers can achieve unparalleled precision and consistency, making it an ideal choice for intricate applications where dimensional accuracy is paramount.
Eccentric vs. Concentric Cones: Understanding the Distinctions
Before delving further into fabrication techniques, it’s essential to grasp the disparity between eccentric and concentric cones:
- Eccentric Cone: In an eccentric cone, the major opening and minor opening are situated on different axes, posing unique challenges in fabrication due to the asymmetrical nature of the geometry. Consequently, eccentric cones are often manufactured in two halves to mitigate complexities associated with forming and welding.
- Concentric Cone: Conversely, a concentric cone features the major opening and minor opening aligned along the same axis, simplifying the fabrication process compared to eccentric counterparts. The symmetrical design facilitates uniform bending or pressing, resulting in a smoother manufacturing workflow.